The Ultimate Guide to Choosing the Right Packaging Machine Repair Experts
The Ultimate Guide to Choosing the Right Packaging Machine Repair Experts
Blog Article
The Ultimate Overview to Packaging Machine Repair Service: Maintain Your Procedures Running Efficiently
Understanding the intricacies of packaging equipment repair work is critical for maintaining optimal efficiency and lessening disruptions. Normal maintenance not only prolongs the life of these devices but also addresses typical problems that can hinder productivity.
Relevance of Routine Maintenance
Normal maintenance of product packaging equipments is vital for making certain optimal efficiency and long life. By executing an organized maintenance routine, operators can recognize possible concerns prior to they intensify into substantial issues. This positive method not only reduces downtime but likewise prolongs the life expectancy of the devices, inevitably bring about minimized operational expenses.
Normal assessments permit for the evaluation of vital parts such as sensors, seals, and belts. Resolving wear and tear without delay avoids unanticipated failures that might disrupt manufacturing and lead to expensive fixings. Additionally, regular maintenance assists make certain conformity with market requirements and policies, fostering a secure workplace.
In addition, upkeep tasks such as cleaning, lubrication, and calibration considerably enhance machine efficiency. Improved performance translates to regular item high quality, which is important for keeping customer fulfillment and brand reputation. A well-maintained packaging equipment operates at optimal speeds and decreases material waste, adding to total efficiency.
Usual Product Packaging Machine Concerns
Packaging equipments, like any complex machinery, can encounter a selection of usual issues that may hinder their efficiency and performance - packaging machine repair. One widespread problem is irregular sealing, which can result in product perishing and wastefulness if bundles are not effectively sealed. This commonly results from misaligned parts or worn sealing elements
One more regular problem is mechanical jams, which can happen because of international objects, worn parts, or improper alignment. Jams can cause delays in manufacturing and increase downtime, eventually affecting overall productivity. In addition, digital malfunctions, such as failure in sensors or control systems, can lead and disrupt operations to incorrect dimensions or erratic equipment behavior.
In addition, concerns with item feed can likewise emerge, where items may not be supplied to the packaging area regularly, causing disturbances. Wear and tear on rollers and belts can lead to suboptimal efficiency, needing immediate interest to protect against further damage.
Comprehending these common issues is essential for keeping the stability of packaging operations, guaranteeing that equipment runs smoothly and successfully, which in turn assists in meeting production targets and preserving item quality.

Repairing Strategies
Effective repairing strategies are necessary for immediately dealing with concerns that occur with product packaging makers. A systematic technique is essential for identifying the origin of breakdowns and minimizing downtime. Begin by collecting information regarding the symptoms observed; this might include uncommon noises, operational hold-ups, or mistake codes displayed on the maker's interface.
Following, refer to the device's handbook for repairing standards details to the version in inquiry. This source can give useful understandings right into common problems and recommended analysis steps. Utilize visual assessments to look for loose connections, worn belts, or misaligned parts, as these physical aspects commonly add to functional failings.
Apply a procedure of removal by testing private machine features. As an example, if a seal is not creating appropriately, evaluate the securing device and temperature settings to identify if they meet functional requirements. File each action taken and the results observed, as this can help in future repairing initiatives.
Repair work vs. Replacement Decisions
When faced with equipment breakdowns, determining whether to fix or replace a product packaging maker can be a complicated and important selection. This decision rests on a number of key aspects, including the age of the device, the degree of the damages, and the projected influence on operational effectiveness.
First of all, consider the machine's age. Older equipments might call for even more regular repairs, bring about greater collective costs that can go beyond the investment in a brand-new device. Furthermore, examine the extent of the malfunction. Small issues can typically be resolved promptly and affordably, whereas substantial damage may demand a substantial economic commitment for fixings.
Operational downtime is another essential consideration. If fixing the maker will create long term hold-ups, investing in a new machine that provides boosted performance and integrity may be extra prudent. In addition, consider the availability of parts; if substitute components are hard to come by, it might be more tactical to change the device completely.
Ultimately, carrying out a cost-benefit analysis that includes both prompt and long-term implications will aid in making an educated choice that aligns with your monetary restrictions and functional goals. (packaging machine repair)
Safety Nets for Longevity
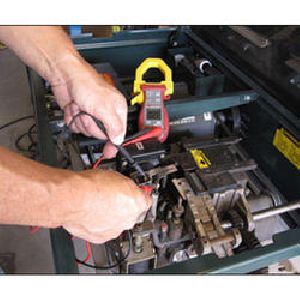
Trick preventative measures include regular lubrication of relocating parts, positioning checks, and calibration of sensors and controls. Establishing a cleansing routine to eliminate particles and impurities from machinery can considerably decrease deterioration (packaging machine repair). Furthermore, keeping track of functional specifications such as temperature and vibration can assist spot abnormalities early
Training team to identify signs of wear or malfunction is an additional important element of preventive maintenance. Equipping operators with the knowledge to execute fundamental troubleshooting can cause quicker resolutions and lessen operational disturbances.
Documentation of maintenance tasks, including visit this site solution documents and evaluation searchings for, cultivates responsibility and promotes notified decision-making pertaining to repairs and substitutes. By prioritizing preventive measures, businesses can ensure their product packaging machines operate at peak performance, eventually resulting in raised efficiency and minimized functional expenses.
Verdict
In final thought, the effective maintenance and repair service of packaging devices are extremely important for sustaining operational effectiveness. By implementing preventative steps, organizations can boost maker durability and make sure uninterrupted productivity in packaging operations.
Understanding the complexities of product packaging maker fixing is vital for maintaining optimal efficiency and lessening interruptions.Regular maintenance of product packaging machines is crucial for guaranteeing ideal efficiency and long life.Product packaging devices, like any kind of intricate machinery, can encounter a selection of common issues that might prevent their efficiency and efficiency. If repairing the device will certainly create prolonged delays, spending in a new machine that supplies improved performance and integrity may be a lot more over at this website prudent.In verdict, the reliable maintenance and repair work of product packaging makers are vital for sustaining functional additional resources performance.
Report this page